|
The (huge) Hyperscript "Iron, Steel and Swords" contains a lot about steel. Check it if you like |
| |
 |
The "Iron
Age" lasted a long time. It actually should be called "Steel
age", because pure iron is not only difficult to make, but has only limited limited
use as a structural material. |
|
 |
Steel and cast
iron, both Fe - C alloys or compounds, and not just iron
made the difference to the bronze tools and weapons in use before the iron age. Note, however, that bronze products were
used for a long time parallel to steel products. |
|
 |
The beginning of the iron age in Northern Europe dates to about 800 BC; one could debate if it ever
really ended. The industrial revolution in the 19th century has one of its deeper roots in the discovery of how steel
could be mass produced; and the car industry, for example, is still perfectly impossible without steel but quite possible
without Silicon. The computer, of course, is perfectly impossible without Si - but does this mean that we are now
in the Silicon Age? |
 |
Iron technology was invented in the Mediterranean about 1500 BC; present day knowledge
ascribes its discovery to the Hethites from what is now Turkey. |
|
 |
India and China also mastered iron technology in ancient times. It appears, however, that the Hethites
were earlier by several hundred if not 1000 years. The Japanese, of course, had and still have a heavy cult around
their steel swords for a longe time, and there was some early iron techology in Africa, too. |
 |
In the "Hyperscripts of AMAT", a growing number of modules deals with the history
of iron and steel; in particular with the ancient paradigm of this material: the (magical) sword.
These modules will give you an idea of what iron technology meant to our ancestors, and why your conception about it is
probably totally wrong. Available are: |
|
 |
A short history of Iron and steel |
|
 |
Myths around making a sword (In German; not
for the faint of heart) |
|
 |
The Ring of the Nibelung (In German; Wagner's
opera in the context of forging Siegfrieds sword). |
|
 |
Damascene Technology (In English;
contains many links to other sources). |
|
 |
An early (magical) sword (In English;
shows the original and its reconstruction). |
|
 |
Magical swords (In German; What makes a sword
magical - how is a Japanese sword made?). |
 |
In this module, however, we will look at steel from a scientific point
of view. |
|
 |
This is not easy: Steel is an extremely complicated material with an amazingly large number of variants;
and new discoveries are still being made. |
|
 |
Here we will only look at some basics; this involves cutting corners
and being at bit imprecise at times. To simplify things, we will treat carbon steels, alloy steels, and cast iron separately;
even so this does not make much sense for many real steels. |
| | |
|
The Iron - Carbon Phase Diagram |
| |
 |
The Iron - Carbon Phase Diagram is one of the most important diagrams of mankind - but not
part of public education. |
|
 |
Here is the important part: |
|
|
|
 |
What we see is: |
|
 |
The color a smith sees at the temperature given (sort of). Notice the "bright cherry red" at the 996 K boundary |
|
 |
Absolutely pure iron changes from the a-phase
(which has a bcc lattice) to the fcc g- phase just below 1200 K (1180
K, to be precise). Around 1700 K it changes to the bcc d-phase; at 1800
K and some it melts. |
|
 |
There is no b Phase ??? Well - b
-ferrite is simply non-magnetic a - ferrite; here we can just forget about it. |
 |
The situation is quite different with a little bit of carbon - somewhat more than
0.1 weight %, say. Around the melting point tricky stuff is going on, which we will not consider any more. |
|
 |
Below
996 K (= 723 oC) the iron cannot dissolve all the C and we have some mixture of a-iron
and Fe3C. |
|
 |
Above
996 K, however, the g-phase can keep quite a bit of C in solid solution
up to a maximum of 2% at 1403 K (= 1130 oC). |
|
 |
At about 0.8 % C, we have an eutectoid composition at a temperature of 966 K, and around 4.5 % we have a true eutectic
composition at 1403 K. |
|
 |
The diagram extends only to about 6.7 % C; at higher C concentration nothing
of interest will be found. This means we are actually considering the Fe - Fe3C phase diagram.
|
|
 |
If you wonder why so much happens with so little carbon, don't forget: At 6.7 weight
%, every fourth atom in the soup is a carbon atom; we have 25 atom %! |
 |
All important true phases have (old) names; these are
- Cementite (German: Zementit). The stoichiometric Fe3C
phase. It is a compound with a complicated lattice; it is rather hard and brittle.
- Ferrite (German: "Ferrit). The a-phase
with the bcc lattice. If you want to be precise, you call it a - ferrite.
- Austenite (German "Austenit). The g-phase
with the fcc lattice.
|
 |
Just to get you used to the facts of life concerning iron and steel, there are
some more old-fashioned names still very much in use, and absolutely de rigeur for everybody who calls herself a materials
scientist:
- Pearlite (German: Perlit), the two-phase mixture obtained
right below the eutectoid point at 0.8 % C concentration - we will encounter
it quite soon and excessively.
- Ledeburite (German: Ledeburit); the two phase mixture
obtained right below the eutectic point at 4.5 % C concentration; we will not
have much dealing with that because it should not exist in equilibrium at room temperature.
- Martensite (German: Martensit); a kind of metastable
version of austenite + carbon; but with a tetragonal lattice and different mechanical
properties; this will exercise us a great deal.
- Bainite (German: Bainit); a mixture of a
- ferrite supersaturated with carbon and cementite, but in a (non-equilibrium) structure
quite different from pearlite.
|
|
 |
If you wonder why there are so many strange
names, consult the link. |
 |
Considering cast iron, the important part is the
eutectic at around 4.4 % C. |
|
 |
At that concentration, casting at about 1400 K is easy; and the temperature is so low
that it was easily achieved in ancient times. |
|
 |
But cast iron contains a lot of carbon
(mostly in the form of graphite; which is not directly evident from the phase diagram),
is brittle, and while employed in huge quantities, not what we are after. What we are
after is steel. |
 |
That is different from an eutectic reaction, where both
components need to solidify. Here nothing needs to solidify, we have some grain structure with a
and b grains, and the a grains could remain unchanged. |
|
 |
We won't go into more details here, but you can look at an illustration of the solidification and phase change process in an illustration module. |
 |
What the structures (= Gefüge)
you get look like is shown in the pictures below. |
|
|
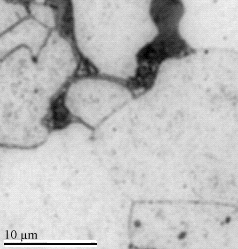 |
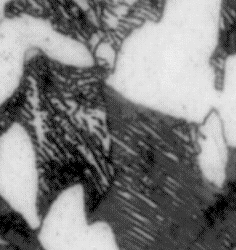 |
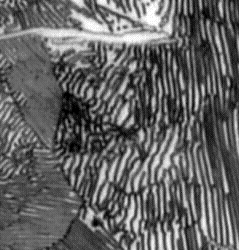 |
Ferrite and blackish Pearlite grains at 0.1 % C |
Ferrite and more blackish Pearlite grains at 0. 4% C |
Pearlite and (white) cementite at 1.3% C. |
Interestingly, cementite seems to be black for hypoeutectice steel and white for hypereutectic steel. Six
sources ignore the obvious problem with pictures like these. The resolution of the apparent paradox (probably) is as
follows: Both, ferrite and cementite are "white". The black part comes from the boundaries
between ferrit and cementite (a simple optical effect at high magnifications). |
|
 |
Now there is a first complication: If we start well above the eutectoid
temperature of 996 K, the composition of the a + g,
or the g + Fe3C phase mix has to change according to the lever rule as the
temperature decreases. |
|
 |
It only can do so by diffusion in the solid state. But
this is a relatively slow process, so we might expect that what we will get, will depend on the cooling
rate. Only for very slow cooling will we obtain the "equilibrium" structure shown in the phase diagram. |
 |
What kind of mechanical properties do we expect? We have, after all, some kind
of composite made from a relatively soft and ductile material (ferrite) and a hard and brittle material (cementite). |
|
 |
As far as Youngs modulus is concerned we could use the rules
derived for compound materials. |
|
 |
But we are more interested in properties like hardness, yield stress, ultimate tensile strength,
and maximum strain. The latter is a kind of direct measure for ductility. Since all these properties are "defect sensitive"
(as we learned in chapter 8!), simple rules cannot exist. We only can make educated guesses. |
| |
 |
We certainly would expect that an increasing cementite concentration would
lead to an increase in hardness but to a concomitant loss of ductility (it becomes hard and brittle). |
|
|
|
 |
Let's see what we get. Some essential mechanical properties are shown on the
right. Since not only the carbon concentration, but also other structural details determine what you get, the graphs give
a whole ranges of properties for structures somewhere between "annealed" and "normalized". |
|
|
 |
"Annealed" and "normalized" refer to different standardized heat treatments
designed to give comparable structures with respect to grain size and shape, and dislocation density. |
|
|
 |
"Annealed" is as close to equilibrium as possible. We have large grains and small
dislocation densities. "Normalized" means that some heat treatment was used so that the history of the material
(it might have been heavily deformed, for example), is essentially wiped out, but grain sizes are small and we are far from
equilibrium. | |
 |
The first graph shows the yield
stress RP (German: Fließgrenze) and the ultimate tensile strength RM (German: maximale Zugfestigkeit). |
|
|
 |
We see that both increase with increasing carbon content, but the more important parameter
RP sort of tapers off and remains constant around 0.5 % C |
|
 |
The second graph gives the maximum elongation that can be achieved in a tensile
test and the impact energy or fracture energy (German:
Zähigkeit). | |
|
 |
The maximum elongation is a fairly direct measure of ductility; we see that the ductile behavior
gets worse in a rather linear fashion with increasing carbon content. |
|
|
 |
It is pretty close to zero as soon as there is no longer a contingent matrix of ductile a- ferrite. | |
|
|
The impact energy is a fairly direct measure of "brittleness". Low energy means
easy fracture - the material is brittle. | |
|
 |
It decreases steeply, tapers off around around 0.5%, and reaches a relatively constant
low value for hypereutectic steels. Essentially, the fracture toughness than is determined by the fracture properties of
the cementite, which now forms a continuous skeleton with embedded pearlite grains 1). |
|
|
| | |
|
 |
So much for the simple part. Iron-carbon compounds
or plain carbon steels now become difficult for two major and related reasons: |
 |
1. The phase diagram from above does not show the real equilibrium structure - FeC3 called cementite
is not the phase with the absolute minimum of the free energy; that is actually carbon. |
|
 |
However, FeC3 is metastable; it simply forms before pure C
(= graphite) can develop; and it may take a long time before all FeC3 is decomposed into C. |
|
 |
The real, i.e. true equilibrium phase diagram of Fe and C, however, looks a
lot like the C - FeC3 from above. Just take out the vertical line for
stoichiometric FeC3, substitute "C" for "FeC3" everywhere,
and shift the horizontal lines downwards a few K; leaving everything else the same (except for the "L + graphite"
liquidus line, which goes up much steeper). If you can't imagine this, look
it up in the link. |
|
 |
This has some consequences for cast iron (it is essentially
the reason why we find pure graphite and not just cementite in cast iron as already mentioned
above) |
 |
2. The solubility of carbon in austenite is much larger than in ferrite.
At temperatures somewhat higher then the "magical" 996 K, austenite can easily accommodate any carbon concentration
around the eutectoid concentration of 0.8%. |
|
 |
Passing the eutectoid temperature during cooling now requires a radical change. Practically
all the homogeneously dissolved carbon now has to go to the inhomogeneously distributed cementite - by diffusion, there
is no other way. |
|
 |
This simply takes time, and if that time is not
available, because the austenite is quenched, i.e. rapidly
cooled (really rapidly at this point, with at least 1000 K/s for hypoeutectics), something new
happens. |
|
 |
The carbon stays in place - more or less - and this necessarily prevents
pearlite and ferrite formation. Instead, a new lattice type is found, called "martensite".
It is a body-centered tetragonal lattice;
essentially a bcc lattice elongated somewhat in one direction. |
 |
The transformation from the fcc austenite
lattice to the tetragonal martensite lattice does not need long range diffusion (as,
e.g., the transformation from the austenite lattice to pearlite). |
|
 |
It takes place by a shear process (involving special dislocations);
and all transformations of that kind are called martensitic
transformations. There are many martensitic transformations in materials science.
|
 |
It looks like martensitic transformations are easy - if you don't have to move
atoms around, it could just happen! |
|
 |
Not so: Changing from one lattice type to another one will (almost) always involve a volume
change. If there is no moving around of atoms, if nothing can "give", such a transformation will then automatically
produce a lot of stress and strain, and thus requires plenty of energy. Martensitic transformations therefore are difficult; they only happen if there is a large driving force. |
|
 |
As a corollary, martensitic structures are rarely equilibrium structures; they are metastable
at best. But that does not mean that they can last a long time at normal temperatures. |
 |
The pictures below illustrate what happens and what it looks like. |
| |
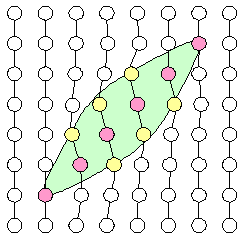 |
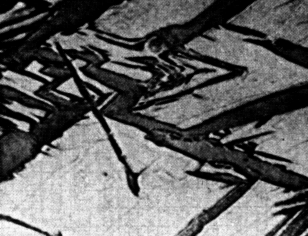 |
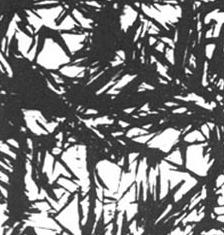 |
The martensite shear transformation |
Martensite "needles" or lathes in austenite (Magnification ×1000) |
|
|
 |
Looking at the schematic representation of the shear transformation; it is clear that the
process is not easy, stores a lot of elastic energy, and tends to make thin needles or plates (called "lathes"). |
 |
Pure martensite is soft and ductile. However, we don't have pure
martensite; we have martensite with interstitially dissolved carbon - and this is an extremely hard and brittle substance.
|
|
 |
Hard martensite is of not much use by itself - but it is the key to things like
"magical swords" or high strength steels
|
 |
Look at the Vickers hardness
diagram below to get an idea of how much better the edge of a Japanese swords - pure martensite - will be, compared to a regular decent steel.
|
|
 |
If you want to know what "hardness"
means in some detail - look up the link above. For steel, the Vickers hardness HV is pretty much
the same thing as the yield stress RP; we have in a good approximation |
| |
|
 |
So in all the diagrams here or in books, you can always substitute hardness for
yield stress and vice verse at least qualitatively. For numbers you have to watch out what kind of hardness (usually Vickers
or Brinell) is given |
| |
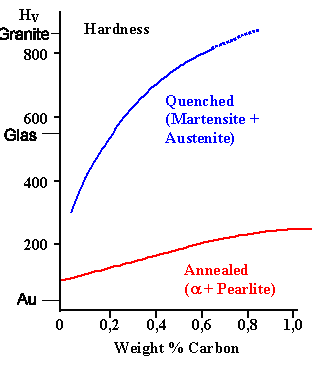 |
|
Vickers hardness of annealed and quenched plain carbon steel. |
Yield stress as function of martensite induced dislocation density |
|
 |
Why is martensitic steel so hard? A better
question is: Why is the yield stress so high, because this addresses basic mechanisms
we learned about in chapter 8? |
|
 |
Above we said because carbon containing martensite is hard - but that is a bit of a tautology. |
 |
Do we need new mechanisms for raising the yield stress of a given material that
we did not address in chapter 8? |
|
 |
As you would guess: Not really! Martensite formation simply generates a high density of dislocations
since a lot of (local) plastic deformation is needed to accommodate the martensite "lathes" |
|
 |
Indeed, if we plot the yield stress (or hardness) versus the root of the dislocation density
introduced by various martensitic structures, we obtain exactly the straight line we would expect from the discussion in
chapter 8.3.4 |
|
|
While this kind of knowledge is not (yet) very helpful if you actually make
steel; it simply proves that we understand what is basically going on - and therefore also what can go wrong. |
| |
|
|
Steel Making Now and Then
|
| |
 |
So, if you were an ancient smith and you would quench your red-hot sword blade
in cold water, you might on occasion find that the edge of the sword is now extremely hard, while the interior is still
tough, but far softer. |
|
 |
What has happened then is easy to see - for us: Only the surface near parts will
cool down fast enough for martensite formation. The inner parts simply will stay hot longer and just produce pearlite with
ferrite or cementite. |
 |
But this will only work on occasion. Why it
does not always work, you don't know. Your best guess would be that some magic is involved, or that some goods need to be
in a good mood on quenching day, if things are to work out. |
|
 |
Because what you ancient smith - living sometime between 1500 BC to 1850 AD
- can't know, is that what you get also depends very much on the exact carbon content (which, whatever it was when you started,
you changed a lot simply by forging the blade in your fire). |
|
 |
Even worse: What you get also depends a lot on all the other elements that your raw steel
will contain in some small amounts. And on the temperature you quench from. And on the temperature you quench to. And on
the liquid you use, not to mention if you agitate it it or don't. And on the clay, or whatever you use to coat parts of
the blade. |
|
 |
And no god, priest, nobleman, politician, philosopher, general, or feuilleton writer ever told you anything
helpful for about 3000 years of steel technology; notwithstanding all the sacrifices, spells, offerings, prayers,
tithes, etc. that you made or were forced to make, and their ever-present air of general superiority. |
|
 |
For all you know, and for all the bullshit they did tell you (try Aristotle):
Some of your products might be good, some might be bad. And nobody really knew why. |
 |
Thank god scientists and engineers, we
don't have to slit the throat of some living being anymore so that some macho or tussy up in the heavens or down in the
netherworld feels obligated to help us to produce good steel on occasion. We know almost
everything there is to know about martensite formation in plain carbon steels. Not yet everything
there is to know, but enough to turn martensite into full scale use for special steels. In particular we know three
major tricks that help us to produce a wide variety of steels reproducibly and reliably: |
|
 |
1. We can produce martensite with rather low cooling
rates, too. All we have to do is to add some suitable elements (which will bring us to the next
subchapter dealing with alloy steel). This will allow us to produce homogeneous martensite
even in bulky steel. That's nice, but still not of much use. |
|
 |
2. We can anneal the material in
a well-defined way; i.e. heat it up again. Since martensite is only metastable, we can expect that at enhanced temperatures
we will get some change to the stable cementite + ferrite mixture. If we do it right, we will retain some of the hardness
of the martensite while gaining some of ductility of low-carbon steel. |
|
 |
3. During cooling, we can keep the steel at some medium to high temperature for a while (this process is called tempering (from German)) - and produce yet another structure. |
 |
For the second point, all that needs to be done is to get the carbon in the austenite
mobile again, so it can form cementite and ferrite. |
|
 |
Obviously, you want to stay below the eutectoid temperature for this; 300 oC
- 600 oC is what you use. |
|
 |
You won't get pearlite + ferrite, however. You rather end up with small FeC3
(= cementite) particles in a-ferrite. Your grain size is also smaller, because you retain
the small grain structure of the martensite. |
|
 |
What you are doing now is optimizing precipitation hardening.
The fine FeC3 particles make dislocation movement difficult (which gives a high yield stress and hardness),
but do not completely prevent it (which keeps the material ductile). |
 |
But don't "over-temper"! If the cementite particles get too coarse,
you loose hardness without gaining much ductility anymore. |
|
 |
If you do it just right, you end up with tempered steel, a synonym for the ultimate combination in strength, hardness, toughness - you name it
- for a good part of the 19th and 20th century. |
 |
By now you got the idea: The exact structure of the cementite - a-ferrite
mixture is of prime importance. We have all the strengthening mechanisms discussed in chapter 8 in combination; in
addition we keep microcracks from happening or spreading. What you get will depend sensitively on the carbon concentration,
and in particular at the heat treatment (cooling and annealing / tempering). |
|
 |
Very slow cooling gives an equilibrium structure with largish grains 1)
of pearlite and ferrite. For low carbon concentrations (say 0.1% - 02 %) we get mediocre strength properties of this
"mild" steel. However, the material is easy to work with and it can be welded! That's why your car body and much
else is made from this basic kind of steel (however, with a few more alloying elements thrown in). |
|
 |
Rapid cooling plus tempering gives "tempered steel". The ultimate in strength for
plain carbon steel, but not easy to work with; it is also not weldable. |
 |
How about rapid cooling to some intermediate temperature; and slow cooling after
that? Followed by some tempering or not? |
|
 |
You get the idea once more. There are innumerable possibilities for plain carbon steel; and
then we have the whole periodic table for alloying - but essentially we understand what is going on. |
 |
The "rapid cooling to some intermediate temperature
and slow cooling after that" suggestion is actually a good one. It produces yet another characteristic mix
of FeC3 - a-ferrite, called "Bainite". |
|
 |
The picture below shows some transmission electron microscope pictures of the structures discussed: |
| |
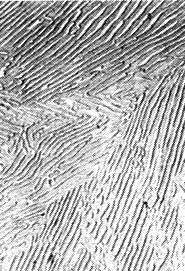 |
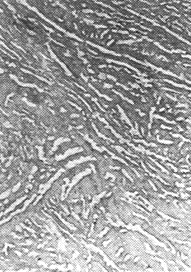 |
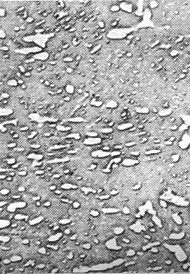 |
Pearlite | Bainite |
Tempered martensite |
|
|
 |
Pretty much the same mixture of Fe and C, but different structures and very different properties |
 |
As promised, we only did some basics - there is much, much more to plain carbon
steel! |
 |
Now we look at all that stuff from a "distance" and realize that what
we do when we make plain carbon steel is just what some ancient smiths did: We used "damascene technology": We
always produced an intimate mix of "soft" and "hard" iron. But there are differences: |
|
 |
We do it on a much finer scale and in far more tricky ways. We also understand what we do.
We don't need magic of any kind or help from above (or below). |
|
 |
We also know how to define and measure the properties of the steel we make. We do not have
to cut through live people to assess the quality (as the Japanese
did). |
 |
But for many kinds of the steel we can make, we have essentially the same problem
as our elders: We cannot cast everything we want. |
|
 |
While we can easily achieve the needed temperatures, just pouring some liquid Fe - C
mix in a form will not give the structure we need. Maybe some additional heat treatment helps, but if not - then you bang
your material into shape like all smiths before you |
|
 |
If you can't cast it, you also will have a hell of a time to weld it. After all, welding means
to liquefy portions of your material and then solidify again. If the structure at the seam is not what you need, you have
a problem. |
 |
This is the main reason while car bodies, to give one example, are not made from
very strong steel. |
|
 |
If instead of pressing sheets of the stuff into the right shape and then weld everything together
you would have to bang it out of some big lump of steel with a hammer, you and I and most everybody else would not be driving
a care. |
|
 |
So be glad we have mild steel and understand
its properties perfectly. Otherwise, the parts of society mentioned above would do what
they always do and did: They drive a car, and you and me
do the banging - as slaves. |
© H. Föll (MaWi 1 Skript)