|
10. 5. Iron and Steel in "Modern" Europe |
|
10.5.1 From Bloomeries to the Blast Furnace |
|
Changes Over Time - a General View |
 |
In the preceding subchapters I covered the early
history of iron and steel in some detail: from the beginning to about Roman times in Europe, or up to - roughly - 400 AD.
Other parts of the world were mostly neglected with the exception of a short
entry for China, and a not-so-short subchapter
about crucible steel in India and parts of Asia.
|
|
 |
There was no iron and steel in the Americas
and Australia before the "white man" brought it along, so there is nothing
to tell. Africa, however, does have a "modern" iron and steel history; I deal
with it - shortly - here. What follows
is heavily biased towards (Northern) Europe. |
 |
So what has happened with respect to iron an steel development between - roughly
- 400 AD and 1870 AD in Europe? Looking at one of the time lines I have given you
before for smelting, one is inclined to conclude: not much! Bloomeries were still run in the 17th century or even later,
and the basic process was not much different from the one used 1500 years earlier. A sword was still forged by a smith.
A 200 BC Celt coming out of some deep freeze in 1500 would hardly note a difference in the forging process. |
|
 |
So the basic techniques for making swords and other iron
/ steel items didn't change much. That is also quite typical for other cultural / technical developments. Does that mean
that the products didn't change much either? Just for fun, let's look at how the changes of products relate to the
changes or non-changes in basic technologies. Here is a first example: |
| |
Same basic technique, quite different product / result |
|
Celtic sculpture, around 400 BC
One of the earliest North-European full-size sculptures |
Uta von Naumburg, middle of the 14th century One of the most impressive Gothic sculptures.
|
Large Picture |
|
The difference (I guess) between using bronze or steel chisels |
|
 |
The basic technique is exactly the same in both cases: take a
rock and chisel off what you don't want. The products display quite different levels of sophistication, however. Progress
comes from attention to details: pick your rock with great deliberation and care, use chisels and hammers of different size
and shapes, learn from a great master, peregrinate around a while and learn from other masters and "schools",
take great care of the final finishing and - most important - practice a lot. |
|
 |
The basic technique of making iron and steel
remained exactly the same for for at least 2000 years: bloomeries processed iron ore with charcoal and produced a bloom.
Bloomeries were still run in the 17th century, if not later. The details of how it was done and the quality of the product
changed quite a bit, however. |
 |
Before I get to the development of bloomeries, let's look a the other extreme: Rather different technologies
produce essentially the same product. |
|
|
Different technologies, same idea / product |
|
Baroque plaster cast; Dresden Around 1700 |
Roman mosaic, Copenhagen museum Around 100 AD, I guess |
Large Picture |
|
|
 |
Since I know that you enjoy artwork, here is more
of the above. |
|
It's good to have you back. For our purpose here the example is making
steel. You can do that in many different ways, e.g. by putting carbon into wrought
iron, or taking it out of cast iron. The product is the same, the technologies are wildly
different. You need to invent the blast furnace, making cast iron and fining it before you can make steel in the second
way. |
|
 |
Some things don't change
much at all, however. Here is an example from everyday life: |
| |
No change in production technologies and products (babies) for
untold millennia |
| Nefertiti and two daughters (ca. 1350 BC) |
Source: Photographed in the "Neues Museeum", Berlin |
|
|
For our purpose here the example is black smithing
or forging. A 1900 black smith would have had not much trouble to do his work in a Roman smithy and vice verse. |
 |
Then we have revolutions where
something utterly new appears. Quantum theory, for example, changed humanities way of life rather radically: |
| |
New insights, technologies and products from quantum theory |
|
Hydrogen bomb / nuclear energy; Anti Baby pill; microchip
Internet / computers All are children of quantum theory. |
|
 |
As far as iron and steel are concerned there were many small revolutions and two
big ones. Small revolutions concerned for example the introduction of the blast furnace, the use of coke instead of charcoal,
making wrought iron and steel from cast iron, and so on. Big revolutions occurred around 1870 (Bessemer et al. allowed steel
mass production) and around 1950 (quantum theory allowed understanding). We might also see the direct use of cast
iron as a revolution leading to new technologies that enabled novel products. |
|
 |
Vagn
Buchwald has written a 600 page book
including a million or so pictures on "Iron Steel and Cast Iron before Bessemer"; sort of a sequel to his 370
page opus "Iron and Steel in Ancient Times". The topic: "Iron and Steel in Modern' Europe" of this chapter
is covered extensively in Buchwald's books Read them and then come back. I'll wait. |
|
 |
You also may just read on if you promise not to grumble at what follows. It is comparatively
short and thus biased. I will omit a lot, I will be subjective, and sometimes I might generalize too much. What I will cover
is: - Power by water wheel for blowing, hammering and other jobs around making iron and steel.
- The Stückofen and the Catalan forge as examples for advanced bloomeries.
- The blast furnace, cast iron, and making wrought iron and steel from it.
- What happened around 1870 and beyond.
|
|
Water Wheels as Sources of Power
|
 |
On my exercise bike I can deliver around 100 Watts (W) of power for many hours,
and 150 W for some 30 minutes or so. That's not bad for a guy of my size and age. Athletes can do better, but not very much
better. Your male slave (or your wife) pushing the bellows thus is good for about 0.1 - 0.2 horse powers (1 HP=746 W) for
8 - 10 hours a day. As long as humans were the essential source of power around iron making, the size of the operation was
limited. And no, you do not usually use horses. They are not only far too valuable, they are also to stupid to dig in mines,
to work bellows or to swing a hammer. |
|
 |
One could of course use many humans to get
more power, as the ever inventive British and Americans demonstrated: |
| |
|
Steel engraving of people being punished in a prison in Jamaica in 1837 |
Source: Internet at large |
|
|
 |
Not only did your prisoners and slaves get their daily constitutional by running
a treadmill, they also produced power on the side. The team above will produce about as much
as a valuable horse! But let's be honest: treadmills, horse mills and other contraptions for producing some power were used everywhere throughout antiquity.
The were turned by humans, horses, donkeys and so on - and even by dogs on occasion. |
 |
A water wheel as power source is much better.
It provides easily for 3 - 4 horse powers or more, works without interruption (as long as the water flows), doesn't need
to be fed and to go to the bathroom, and never wails and complains. However, for making a good one, you need iron and steel. |
|
 |
The Romans (and others around their time) did use water wheels for all kinds of things but
apparently not in the iron and steel industry. It was used for moving water up (including in mines), for grinding cereals,
for operating marble saws, and I don't know what else. Constructions like this one (and simpler ones) may have been in used
in the later first millennium BC: |
|
|
|
Water wheels in Hama, Syria, from the 12th - 13th century |
Source: Hama Internet site |
|
|
After the official end of the Roman Empire in 476 things declined for a while but the water wheel technology never
disappeared totally. Eventually it spread over all of Northern Europe, reaching England in the 9th and 10th century and
the more remote corners of Scandinavia and the East in the 11th and 12th century. In the Domesday book from around 1085,
more than 5000 water mills were listed for England alone. The Domesday book, by the way,
records the results of a great survey of much of England and parts of Wales for William I of England, better known as William the Conqueror. He wanted to find out what
and how much each landholder had in land and livestock, and what it was worth, so he could tax it accordingly. The fun of
conquering is always with the conqueror and not so much with the conquerees. |
|
 |
Water wheels were important for mining by then. And mind you, mining did not focus on getting
iron ore - that was more or less all over the place - but on silver, tin or other more precious ores. You needed to move
things, to crush the ore and, most important, to get the water out of the shafts. That takes a lot of power. |
|
As far as iron and steel making is concerned, all of the above helps. Water wheels
were essential for getting and preparing the ore. They also allowed to pump big bellows needed for blowing big bloomeries.
Without them you could not move the big hammers needed to forge the big blooms that will come out of big bloomeries.
The catch is: all the machines needed must be in operation at the same time. Big blooms are useless without big hammers
at the ready. "Man muss das Eisen schmiede solange es heiß ist" (You need to
forge the iron while it is hot) is a well-know old proverb in the true
language of iron and steel. You are now running a demanding business and no longer a I-do-it-when-I-feel-like-it outfit |
|
 |
It appears that it took a few centuries before all the infrastructure that was required besides
just having a water wheel came into existence. What is needed for "power" bloomeries and "power" forges
(as shown below in a 1550 illustration) are the following ingredients:
- A place at a running water that could drive big wheels. It is unlikely that this
place also has iron ore near-by. That forced the bloomeries to move down into the valley from their more lofty uphill places
close to the ore, and to establish the logistics for ore transportation. Charcoal still could be produced in the next forest
typically not far away.
- Big bellows
like these. Those are far more complex machines than the ones a
human could pump.
- A device that transforms
the rotational movement of a water wheel into the up-and-down movement needed for pumping bellows or moving hammers.
Not so easy in ancient times.
- A control
of pumping and hammer movements that are a bit more subtle than just "on" and "off". That necessitates,
for example, a control of the water flow across the wheel.
- A second independent wheel that moves a big hammer
like this one controllably
up-and down.
- The necessary infrastructure for running a big bloomery and the power forge in perfect
synchronization.
|
|
|
|
Water mills power hammers and bellows |
Source: From Olaus Magnus: History of the Nordic Peoples (1555); open access Internet |
|
 |
In other words: Besides being in possession of a lot of know-how you also need
to make quite an investment and to employ a sizeable crew of experienced guys good at
tricky and dangerous team work. And you had to be at it all the time if you wanted a return on investment. You needed to
make a profit not only for your own sake but also for paying off the Mafia (then called nobility). Contrast that to
the small uphill bloomery. You could run that yourself with the help of your family during the vacation time or on long
weekends. You could not loose much cash because most of your investment was the work you and your yokels put into the effort.
At the worst you lost some time, at the best you made cash or saved some because you did not need to buy your iron from
others. Somewhere here is the reason why it took quite a while before big power-blown bloomeries (more or less the
same as a blast furnace) in conjunction with power-hammer forges became the standard. In Agricola's
famed book from around 1550, many water wheels are shown in connection with mining and water control (like pumping)
but only a few times, rather indirectly, connected to blowing or hammering. |
| |
|
Big reversible water wheel for up and down movements
of a load. |
"Power" bellows and a "power" hammer (D); water wheel not shown. |
Water power in Agricola's book
More and large-scale pictures |
|
|
 |
Uses of water power for smelting are recorded for the early 13th century, and it happened
indeed in the 12th and 13th century that bloomeries moved downhill to rivers that could drive water wheels. Power hammers
were definitely in use around 1335 in Spain. In the 15th century the Basque "valley of iron" saw as many as 20
hammer-works in Lagazpi; wherever that might be. Large bloomeries as part of a sophisticated "industrial" infrastructure
could now develop - the next paragraph gives two examples. |
| |
|
|
Stückofen and Catalan Forge |
 |
In Roman times bloomeries were run in a well-organized way; the increase in bloom size encountered in England gives a clear idea about that. While the development
of the bloomery must have gone through ups and downs, they did not seem to have changed very much until the use of water
power allowed making and processing larger blooms. The good old "Ferrum
Noricum" changed its name after the demise of the Roman empire but the iron and steel making tradition around Erzberg / Hüttenberg lived on (until almost today).
Power bellows and hammers took over in the 12th and 13th century and the bloomery furnace became bigger and was made from
sturdy stone masonry, typically with a rectangular cross section. |
|
 |
The only halfway contemporary picture, once more, is from Agricola's book: |
| |
| Stückofen |
|
|
 |
However, Agricola omitted the bellows. They often were right in front but could
be on the backside behind the wall in this case. The lower part (plus possibly the bellows) had to be removed to get at
the bloom, which in German is called "luppe".
That's why a Stückofen is also called a Wolf's Ofen in German. And it's "Stück", not "stuck",
meaning piece, chunk, lump. The Stückofen shown above would have produced something like a 20 kg - 30 kg bloom,
far too large to be forged with 2 kg hammers powered by humans. |
 |
As time went by, the Stückofen grew in size. In 1430 blooms weighing 370
kg were reported - just what you needed to feed to your 500 kg power hammer. Larger and larger Stücköfen automatically
became hotter because of their increasing volume
to surface ratio and if they produced cast iron, you called them blast furnace. In fact, cast iron appeared as an unwished-for
by-product besides the bloom in late Stücköfen. Eventually the iron masters learned to work with that stuff and
the era of cast iron production began; see below. |
|
 |
Meanwhile the Stückofen (actually rather called "Blauhaus"
or "Plahütte" (=Blashaus or blow house) by the
local yokels) reached gargantuan sizes. When the last one in Austria was was finally extinguished forever in 1770, the blooms
had reached masses of 900 kg! |
 |
In many areas in Europe similar developments took place. Similar but not identical.
Each place had its specific technologies, based on tradition and local know-how. Local procedures were optimized by evolution to local conditions, like the kind and quality of the available ore. However, small
revolutions also occurred. One was the invention of the "trompe",
an air blowing device radically different from bellows. Today we call it water
aspirator
and it is an ubiquitous (small) device in many laboratories. The principle is simple: A water jet rushing down a pipe
with an opening in the upper part will suck air down with the jet too, and thus can be used as a pump for evacuating vessels
(today's use), or as a blower creating an air stream. |
|
 |
The trompe appeared around 1620 in Spain and moved up to Southern France and other places.
It was employed in what is called a Catalan furnace or forge. What we know about this
type of bloomery goes mostly back to Southern France, not Catalania. The trompe supplied an especially steady airflow that
could be well regulated. The water vapor coming with the air might have been beneficial, too, since it decomposed into hydrogen
and carbon monoxide at high temperatures. Here is what a Catalan furnace with a trompe looked like: |
| |
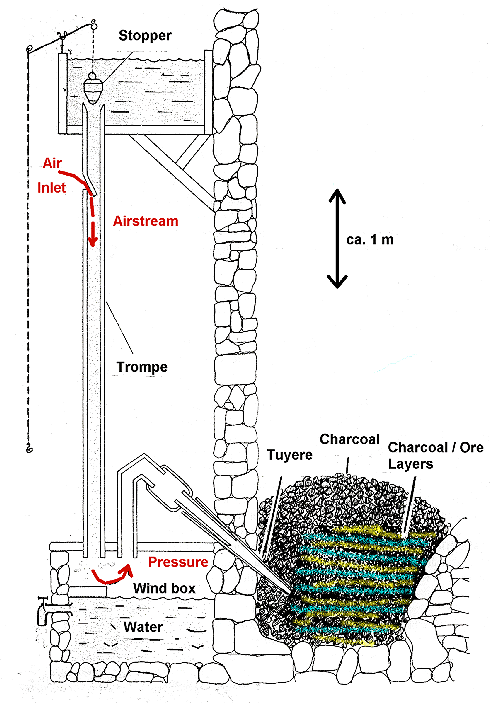 | Catalan forge with trompe |
Source: Libre de la Farga, 1983; via Buchwald. |
|
 |
The trompe is interesting but it never replaced the bellows completely. The Catalan
forge is interesting to us for another reason: the way it was constructed and loaded. It looked more like a squat asymmetric
bathtub than a pipe, and parts of its walls were made form thick cast iron. The ore was divided in two grades: walnut sized
lumps and coarse powder. First the bottom was filled with charcoals up to tuyere level, then (with the help of a temporary
divider) charcoal was piled up close to the tuyere and layers of charcoal, ore lumps and ore powder to the right as schematically
indicated above. The furnace was run on a light blast for the first three hours or so. The slag tapped during this time
was fed back to the smelter. Then the blast was increased and more ore and charcoal added as needed. The charcoal side close
to the tuyere was moistened and compacted with shovels on occasion to avoid gases from escaping there. A big advantage of
the Catalan furnace was that it could be stoked and "worked" from above while it run. The Catalan furnace
was still a bloomery - but with plenty of attention to details! |
|
 |
A bloom of up to 150 kg was recovered through the side by lifting it out
with levers (and with effort!). The process produced three qualities of iron /steel. The inside of the bloom consisted of
soft, almost carbon-free wrought iron, the outside was good hard carbon steel, and the intermediate regions intermediate.
The iron master had many ways to control the product: - Change the ratio of charcoals : lump ore : powder ore.
- Change the tuyere inclination.
- Change the airflow / processing time.
- Change the amount of the manganese oxide that was supplied with some gangue. More of that kind of "gangue"
gives more steel.
|
 |
I gave you these data to illustrate the point I made above: The basic techniques
hardly changed but substantial progress comes from attention to details! |
| |
|
|
The Blast Furnace |
 |
Stückofens, Catalan forges, and just about any bloomery are blast furnaces
in the literal sense oft the word. What the term really means, however, is a furnace
where enough air is blasted in to allow the production of cast iron and nothing
but cast iron (besides slag, of course). The term also implies continuous smelting with high efficiency of even "poor"
ores. In fact, as pointed out before, the slag from ancient Etruscan and Roman
bloomeries was used as a good iron ore and fed into blast furnaces around 1925. Just looking at the making of liquid
and carbon-rich cast iron misses the point, however. Making that in a bloomery type
of furnace was never a real problem, except perhaps for the very early times of iron bloomeries. It appears that European
iron makers simply avoided to do this because the product was not useful to them. It also needed more charcoal and more
efforts at blowing, so why bother? |
|
 |
We know of course that cast
iron is quite useful in two rather different ways:
- Cast iron, though brittle, can be directly used for making all kinds of universally useful things like bathtubs or man-hole covers plus questionable things like cannons and
cannon balls by simply casting the liquid into a mould.
- Cast iron can serve as a cheap raw material for making pure iron and all kinds of steel
We also know that the Chinese made cast iron in blast
furnaces right away and used it for both applications enumerated above. |
 |
In the West, however, cast iron came into its own rather gradually. Power-blasted
bloomeries like the Stückofen or the Catalan forge could easily make cast iron if so desired, and it appears that its
production parallel to a bloom could often not be avoided. |
|
 |
The Austrians in the "Ferrum Noricum" region knew the stuff. Cast iron was produced
on the side in their larger Stückofen; it could be tapped and collected. The Austrians called it "Graglach";
lach containing the German "Lache"=puddle, pool, (small) lake. "Grag" is
unclear, it appears, but I believe it simply comes from "krakelig"=scrawny, spidery; and Graglach is simply a
pool of liquid iron that looks like this: |
| |
|
A "krakelige Lache" (?)=(?) Graglach. Here it happens
to be (now solidified) copper |
Source: Photographed in the Copenhagen museum |
|
|
 |
You can't get much more krakelig than the copper above. Anyway, the old iron guys learned
to do things with the graglach and eventually it became a commodity traded far and wide. In 1469, for example, one Peter
Pögl delivered 14 000 canon balls to Emperor Friedrich III, called the Peaceful, who wanted to play ball with the Hungarians,
Bohemians or the Turks if the first two weren't available. |
|
Meanwhile some other Austrians run a "Flossofen" (German for flowoven)
with know-how imported from Brescia, Italy. A Flossofen was not all that much different from a Stückofen but used only for making cast iron - up to 2000 kg a day! That started in 1570 and that enterprise ran
parallel to making huge blooms around the corner of the river in the Stückofen. I would guess that the Flossofen guys
used calcium carbonate (CaCO3) or limestone as flux, given the large yield of iron they obviously enjoyed, but
I don't really know. Supposedly it was the Durch Jan Andries Moerbeck
who found out around 1619 that the limestone was good for fluxing because he noticed that the English in the "Weald"
were particularly successful in smelting cast iron because their ore was "self-fluxing" and contained limestone
as gangue. With limestone as flux you first form quicklime
(CaO) at high temperatures, which in turn produces some calcium silicate as liquid slag component instead of the good old
iron silicate fayalite that still contained much of the iron from the
ore. The "limestone slag" contains only little iron (around 10 %) instead of about half of what the smelter was
originally fed with in the case of fayalite. |
|
 |
How cast iron and thus the blast furnace came into its own is a tangled story, intermixed
with the development of the gun. You need a lot of metal to make a 1000 kg "bombard" or cannon, and it needs to be "good" metal lest your weapon explodes upon firing. Good bronze
is fine but rather expensive, and wrought iron or steel from a bloomery is not so easily turned into a huge object just
by forging and fire welding; see below. Cast iron would be ideal but you better know how to work with this brittle material
before you cast a gun and fire it. Cast iron, as we know,
comes in many grades and can have a wide range of properties. Don't forget that the technology of metals other than
iron was quite developed in the Middle Age. Large bells were cast from "Speiss",
by then more or less weird copper-centered alloys. Of course people started mixing the new liquid
iron with everything else they could liquefy and a lot of weird and useless stuff must have been produced. Suffice
it to look at a few dates and events (mostly taken from Wertimes
book) just to illustrate what was going on:
- In 1353 Berthold Schwarz invented "black powder"; necessary for guns and cannons. No, he did not! It's a myth.
Knwledge about black powder diffused to Europe from the East (China), and
- Already around 1320 the first guns appeared in Europe.
- 1390 the first recorded casting of a cast-iron cannon took place in Frankfurt/Main, Germany.
- Wesel, a town in North Germany, possessed a cast iron gun in 1400.
- In Burgundy iron cannons were cast (and the fact recorded) between 1414 - 1417.
- Cast iron cannons appeared in Italy in 1429 (plus cast iron pans)
- Siegen in Germany started mass-production of cast iron cannons in 1445.
- On 29 May 1453, after an eight-week siege (during which the last Roman emperor, Constantine XI, was killed), Sultan
Mehmed II "the Conqueror" took Constantinople (afterwards calld Istanbul). A cannon was decisive in destroying
the famous walls of the city.
- But: Neither Agricola
(1556) nor Biringuccio (1540) in their lengthy
books pay much attention to cast iron, even so the latter devotes plenty of space to casting cannons with other
metals.
|
|
|
|
I's not so easy to forge a cannon on a normal smithy hearth |
Source: Donal Duck Sonderheft Nr. 28; with friendly permission of Ehapa Verlag. |
|
 |
People obviously did use cast-iron to cast
cannons, cannon balls, frying pans and much other stuff around 1400 or even somewhat earlier. It the objects were well made,
it didn't matter much that the material was hard but brittle. It still could be strong enough for the purpose. Your porcelain
toilet is perfectly brittle, for example, but can take a lot of punishment. Using cast-iron as a raw material for making
wrought iron and steel of all grades is a different matter, however. You had to take the carbon (and other stuff) out almost
completely in order to get soft wrought iron. If you wanted steel, you had to stop a the right moment in the process of
reducing the carbon concentration (almost impossible) or, if you went all the way resulting in wrought iron, put some carbon
back in. Sounds not only complicated; is complicated - but still worth it, because making cast iron as starting material
had tremendous advantages in comparison to running a bloomery:
- The smelter could be run in a continuous process for days or weeks on end. Keep
feeding your blast furnace with ore, charcoal and flux, keep blowing it steadily, and you can tap your cast iron and the
slag periodically without ever stopping (as long as the walls hold out).
- Size is no longer limited by keeping a bloom from getting too large. You can now make your blast furnace rather large, automatically increasing
efficiency and the output.
- You can use limestone as flux, avoiding fayalite formation. Your slag
thus does not have to contain a lot of iron anymore and efficiency goes up.
- You can use difficult ores - either low grade ore or high-grade but hard, e.g. stuff like magnetite.
- You produce a liquid that you can cast directly
or after remelting!
|
|
 |
With coke replacing charcoal after 1730 (look
it up here) blast furnaces could get even larger. Coke
is mechanically stronger than charcoal and doesn't crumble if the weight of the burden exceeds a certain limit. It is not
as reactive as charcoal but you don't need to cut down your last trees in order to make it. You could dig up plenty of the
coal needed to make coke in the coal mining places. That is the reason why iron smelting now moved to the places where coal
was abundant. |
|
A soon as cast iron was understood, one could make all kinds of machinery and
parts besides cannons. Watt's
steam engine from 1765 could not be imagined without cast iron. In time it provided more power than the water wheel,
and blast furnaces could be made bigger once more. The steam engine also provided sufficient power for blowing air through
liquid cast iron, allowing the Bessemer process and anything else that caused the
industrial revolution that is still going on. In case I haven't mentioned it yet: There can be no silicon technology without
steel. There is plenty of steel inside any semiconductor manufacturing plant. |
|
 |
It's time to stop or I will need to start another Hyperscript, far larger than the present
one. |
|
| |
© H. Föll (Iron, Steel and Swords script)