|
Silicon would not be the "miracle material" without its oxide, SiO2,
also known as ordinary quartz in its
bulk form, or as rock crystal if you find it in single crystal form (and relatively pure)
somewhere out there in the mountains. |
|
 |
Not only the properties of Si - especially the achievable
crystalline perfection in combination with the bandgap and easy doping - but also the properties of SiO2
are pretty much as one would have wished them to be for making integrated circuits and other devices. |
|
 |
From the beginning of integrated circuit technology - say 1970 - to the
end of the millennium, SiO2 was a key material that was used for many different purposes. Only now (around
2004), industry has started to replace it for some applications with other, highly "specialized" dielectrics. |
 |
What is so special about SiO2? |
|
 |
First of all, it comes in many forms: There are several allotropes
(meaning different crystal types) of SiO2 crystals; the most common (stable at room temperature and ambient
pressure) is "low quartz" or a-quartz, the quartz crystals found everywhere.
But SiO2 is also rather stable and easy to make in amorphous form. It is amorphous SiO2
- homogeneous and isotropic - that is used in integrated circuit technology. The link provides the phase
diagram of SiO2 and lists some of its allotropes. |
|
 |
SiO2 has excellent dielectric properties.
Its dielectric constant
er is about 3.7 - 3.9 (depending somewhat on its structure). This was a value large enough to allow decent capacitances if
SiO2 is used as capacitor dielectric, but small enough so that the
time constant R · C (which describes the time delay in wires having a resistance R
and being insulated by SiO2, and thus endowed with a parasitic capacitance C that scales
with er) does not limit the maximum frequency of the devices. It is here that
successors for SiO2 with larger or smaller er values are
needed to make the most advanced devices (which will hit the market around 2002). |
|
 |
It is among the best insulators known and
has one of the highest break-through field strengths of all materials investigated so
far (it can be as high as 15 MV/cm for very thin layers; compare that with the values
given for normal "bulk" dielectrics). |
|
 |
The
electrical properties of the Si - SiO2 interface are excellent. This
means that the interface has a very low density of energy states (akin to surface states) in the bandgap and thus does neither
provide recombination centers nor introduce fixed charges. |
|
 |
SiO2 is relatively easy to make
with several quite different methods, thus allowing a large degree of process leeway. |
|
 |
It is also relatively easy to structure, i.e.
unwanted SiO2 can be removed selectively to Si (and some other materials) without many problems. |
|
 |
It is very stable and chemically inert. It
essentially protects the Si or the whole integrated circuit from rapid deterioration in a chemically hostile environment
(provided simply by humid air which will attack most "unprotected" materials). |
 |
What are the uses of SiO2? Above, some of them were already
mentioned, here we just list them a bit more systematically. If you do not quite understand some of the uses - do not worry,
we will come back to it. |
|
|
|
 |
Gate oxides: As we have seen
before, we need a thin dielectric material to insulate the gate from the channel area. We want the channel to open at
low threshold voltages and this requires large dielectric constants and especially no charges in the dielectric or at the
two interfaces. Of course, we always need high break through field strength, too. No dielectric so far can match the properties
of SiO2 in total. | |
- Gate oxide for Transistors
- Dielectric in Capacitors
- Insulation
- Stress relieve layer
- Masking layer
- Screen oxide during Implantation
- Passivation
|
|
|
 |
Dielectrics in integrated capacitors. Capacitors
with high capacitance values at small dimensions are needed
for so-called dynamic random access memories (DRAM), one of
the most important integrated circuits (in terms of volume production). You want something like 30 fF (femtofarad)
on an area of 0.25 µm2. The same issues as above are crucial,
except that a large dielectric constant is even more important. While SiO2 was the material of choice
for many DRAM generations (from the 16 kbit DRAM to the 1 Mbit DRAM), starting with the 4 Mbit
generation in about 1990, it was replaced by a triple layer of SiO2 - Si3N4
- SiO2, universally known as "ONO" (short for
oxide - nitride - oxide); a compromise that takes not only advantage of the relatively large dielectric constant of silicon
nitride (around 7.5) while still keeping the superior quality of the Si - SiO2 interface, but has
a few added benefits - at added costs, of course. | |
|
 |
Insulation: Some insulating material is needed between
the transistor in the Si as well as between the many layers of wiring on the chip; cf. the many pictures in chapter four, starting with the one accessible via the link. SiO2
was (and still is) the material of choice. However, here we would like to have a material with a small
dielectric constant, ideally 1, minimizing the parasitic capacitance between wiring and SiO2 may
have to be replaced with a different kind of dielectric around 2003. |
|
|
 |
Stress relieve layer: SiO2
becomes "viscous" at high temperatures - it is a glass, after all. While it
is a small effect, it is large enough to absorb the stress that would develop between unwielding materials, e.g. Si3N4
on Si, if it is used as a "buffer oxide", i.e. as a thin intermediary
layer. | |
|
 |
Masking: Areas on the Si which are not be exposed
to dopant diffusion or ion implantation must be
protected by something impenetrable and that also can be removed easily after "use". It's SiO2,
of course, in many cases, | |
|
 |
"Screen oxides" provide one example of so-called
sacrificial layers which have no direct function and are disposed off after use.
A screen oxide is a thin layer of SiO2 which stops the low energy debris that comes along with the high-energy
ion beam - consisting, e.g., of metal ions that some stray ions from the main beam banged off the walls of the machine.
All these (highly detrimental) metal and carbon ions get stuck in the screen oxide (which will be removed after the implantation)
and never enter the Si. In addition, the screen oxide scatters the main ion beam a little and thus prevents "channeling", i.e. deep penetration of the ions if the beam happens to be aligned with a
major crystallographic direction. | |
|
 |
Passivation:
After the chip is finished, it has to be protected from the environment and all bare surfaces need to be electrically passivates
- its done with SiO2 (or a mixture of oxide and nitride). |
|
|
| |
 |
Enough reasons for looking at the oxide generation process a little more closely?
If you think not - well there are more uses, just consult the
list of processes for a 16 Mbit DRAM: You need SiO2 about 20 times! |
|
In this paragraph we will restrict ourselves to thermal oxidation. It was (and to a large extent still is) one of the key processes for making integrated
circuits. While it may be used for "secondary" purposes like protecting the bare Si surface during some
critical process (remember the "screen oxide" from above?), its major use is in three areas:
|
|
 |
Gate oxide (often known as "GOX") |
|
 |
Capacitor dielectric, either as "simple"
oxide or as the "bread" in an "ONO" (=
oxide-nitride-oxide sandwich) |
|
 |
Field oxide (FOX) - the lateral insulation between transistors. |
 |
We can use a picture from
chapter 4.1.4 to illustrate GOX and FOX; the capacitor
dielectric can also be found in this chapter. |
|
|
|
|
 |
We must realize, however, that those drawing are never to scale.
The gate oxide is only around 10 nm thick (actually, it "just" (2007) petered out at 1.2 nm
accoding to Intel and is now replaced by a thicked HfO2), whereas the field oxide (and the insulating
oxide) is in the order of 500 nm. What it looks like at atomic resolution in an electron microscope is shown in this link. |
 |
There are essentially two ways to do a thermal
oxidation. |
 |
"Dry oxidation", using the reaction
. |
| |
2 Si + O2 |
Þ |
2 SiO2 | |
(800 oC - 1100 oC) | |
|
|
|
 |
This is the standard reaction for thin oxides. Oxide growth is rather slow and easily controllable.
|
|
 |
To give an example: Growing 700 nm oxide at 1000 oC would take about
60 hr - far too long for efficient processing. But 7nm take only about 15 min - and that is now too
short for precise control; you would want to lower the temperature. |
 |
"Wet oxidation", using the reaction
|
| |
Si + 2 H2O |
Þ |
SiO2 + 2 H2 | |
(800 oC - 1100 oC) | |
|
|
|
 |
The growth kinetics are about 10x faster than for dry oxidations; this is the process
used for the thick field oxides. |
|
 |
Growing 700 nm oxide at 1000 oC now takes about 1.5 hr - still
pretty long but tolerable. Thin oxides are never made this way. |
 |
In both cases the oxygen (in the form of O, O2, OH–,
whatever,...) has to diffuse through the oxide already formed to reach the Si - SiO2
interface where the actual reaction takes place. |
|
 |
This becomes more difficult for thick oxides, the reaction after some
time of oxide formation is always diffusion limited.
The thickness dox of the growing oxide in this case follow a general "square
root" law, i.e. it is proportional to the diffusion length L = (Dt)1/2 (D
= diffusion coefficient of the oxygen carrying species in SiO2; t = time). |
|
 |
We thus have a general relation of the form . |
| |
dthick-ox | = |
const. · (D · t)1/2 |
|
|
|
 |
For short times or thin oxide thicknesses (about <
30 nm), a linear law is found |
| |
|
|
 |
In this case the limiting factor is the rate at which O can be incorporated into the
Si - SiO2 interface. |
 |
This kind of behavior - linear growth switching to square root growth - can be
modelled quite nicely by a not too complicated theory known as the Deal-Grove
model. Some results of experiments and modeling are shown below. |
| |
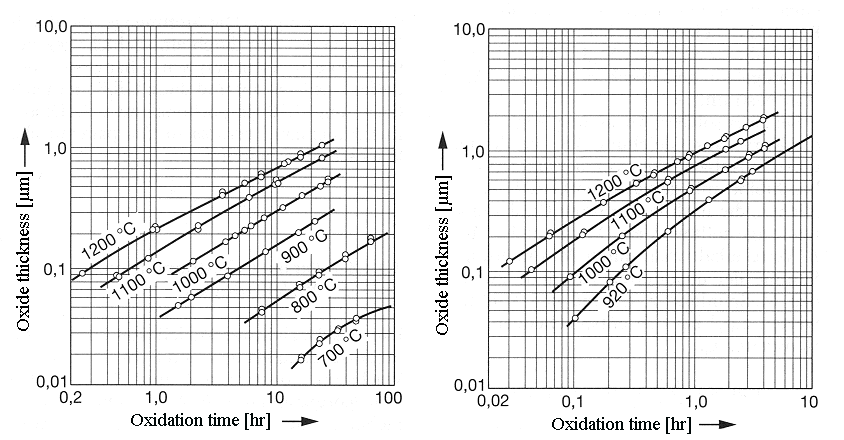 |
Dry oxidation | Wet oxidation |
|
|
 |
The left diagram shows dry, the right hand one wet oxidation. The solid curves were calculated
with the Deal-Grove model after parameter adjustment, the circles indicate experimental results. The
theory seems to be pretty good !. |
 |
However, for very thin oxides - and those
are the ones needed or GOX or capacitors - things are even more complicated as shown below. |
| |
|
| |
|
|
 |
The red points are data points from an experiment (at an unusually low temperature); the blue
curve is the best Deal-Grove fit under the (not justified) assumption that at t = 0 an oxide with a thickness
of about 20 nm was already present. |
|
 |
The Deal-Grove model is clearly inadequate for the technologically important case of very
thin oxides and experimentally an exponential law is found for the dependence of the
oxide thickness on time for very short times |
|
 |
Moreover, the detailed kinetics of oxide growth are influenced by many other factors, e.g.
the crystallographic orientation of the Si surface, the mechanical
stress in the oxide (which in turn depends on many process variables), the substrate doping,
and the initial condition of the Si surface. |
 |
And this is only the thickness! If we consider
the properties of the oxide, e.g. the amount of fixed charge or interface charge, its
etching rate, or - most difficult to assess
- how long it will last when the device is used, things become most complicated. An oxide with a nominal thickness dox
can be produced in many ways: dry or wet oxidation, high temperatures and short oxidation times or the other way around
- its properties, however, can be very different. |
|
 |
We won't look into details here but only use the issue to illustrate an important point when
discussing processes for microelectronics: |
|
 |
Learning about microelectronic processes involves very little Math; and "theory"
is needed only at an elementary to medium level! But this does not make the issue trivial
- quite the contrary. If you would have a theory - however complicated - that predicts all oxide properties as a function
of all variables, process development would be easy. But presently, even involved theories are mostly far too simple to
come even close to what is needed. On an advanced level of real process development, it is the interplay of a solid foundation
in materials science, lots of experience, usage of mathematical models as far as they exist, and finally some luck or "feeling"
for the job, that will carry the day. |
|
 |
So do not consider microelectronic processes "simple" because you
do not find lots of differential equations here. There are few enterprises more challenging for a materials scientist then
to develop key processes for the next chip generation! |
|
How is a thermal oxidation done in real life? Always inside an
oxidation furnace in a batch process; i.e. many wafers (usually 100) are processed
at the same time. |
|
 |
Oxidation furnaces are complicated affairs, the sketch below
does not do justice to the intricacies involved (nowadays they are usually no longer horizontal as shown below, but vertical).
For some pictures of real furnaces use the link. |
| |
|
|
 |
First of all, temperature, gas flow etc., needs not only to be very constant but precisely
adjustable to your needs. Generally, you do not load the furnace at the process temperature but at some lower temperature
to avoid thermal shock of the wafers (inducing temperature
gradients, leading to mechanical stress gradients, leading to plastic deformation, leading to the generation of dislocations,
leading to wafers you have to throw away). After loading, you "ramp up" the temperature with a precisely defined
rate, e.g. 15 oC/min, to the process temperature selected. |
|
 |
During loading and ramping up, you may not want to start the oxidation, so you run N2
or Ar through the furnace. After the process temperature has been reached, you switch to O2
for dry oxidation or the right mixture of H2 and O2 which will immediately
burn to H2O if you want to do a wet oxidation. |
|
 |
After the oxidation time is over, you ramp down the temperature and move the wafers out of
the furnace. |
 |
Moving wafers in and out of the furnace, incidentally, is not easy. |
|
 |
First you have to transfer the wafers to the rigid rod system (usually SiC clad with
high purity quartz) that moves in and out, and than you have to make sure that the whole contraption - easily 2 m
long - moves in and out at a predetermined speed v without ever touching anything - because that would produce particles.
|
|
 |
There is quite a weight on the rods and they have to be absolutely unbendable even at the
highest process temperature around 1150 oC. |
|
 |
Of course, the rods, the quartz furnace tube and anything else getting hot or coming into
contact with the Si, must be ultrapure - hot Si
would just lap up even smallest traces of deadly fast-diffusing
metals. |
 |
And now to the difficult part: After the process
"works", you now must make sure that it works exactly the same way (with tolerances of < 5%) on all
100 wafers in a run in, from run to run, and independently of which one of the 10 or so furnaces is used. |
|
 |
So take note: Assuring stable process specifications for
a production environment may be a more demanding and difficult job than to develop the
process in the first place. |
 |
You see: At the final count, a "simple" process like thermal oxidation
consists of a process recipe that easily calls for more than 20 precisely specified parameters, and changing anyone
just a little bit may change the properties of your oxide in major ways. |
|
All these points were emphasized to demonstrate that even seemingly simple processes in
the production of integrated circuits are rather complex. |
|
|
 |
The processes to be discussed in what follows are no less complex, rather more so. But we
will not go into the finer points at great depth anymore. |
© H. Föll (Electronic Materials - Script)